Fabric Printing Techniques
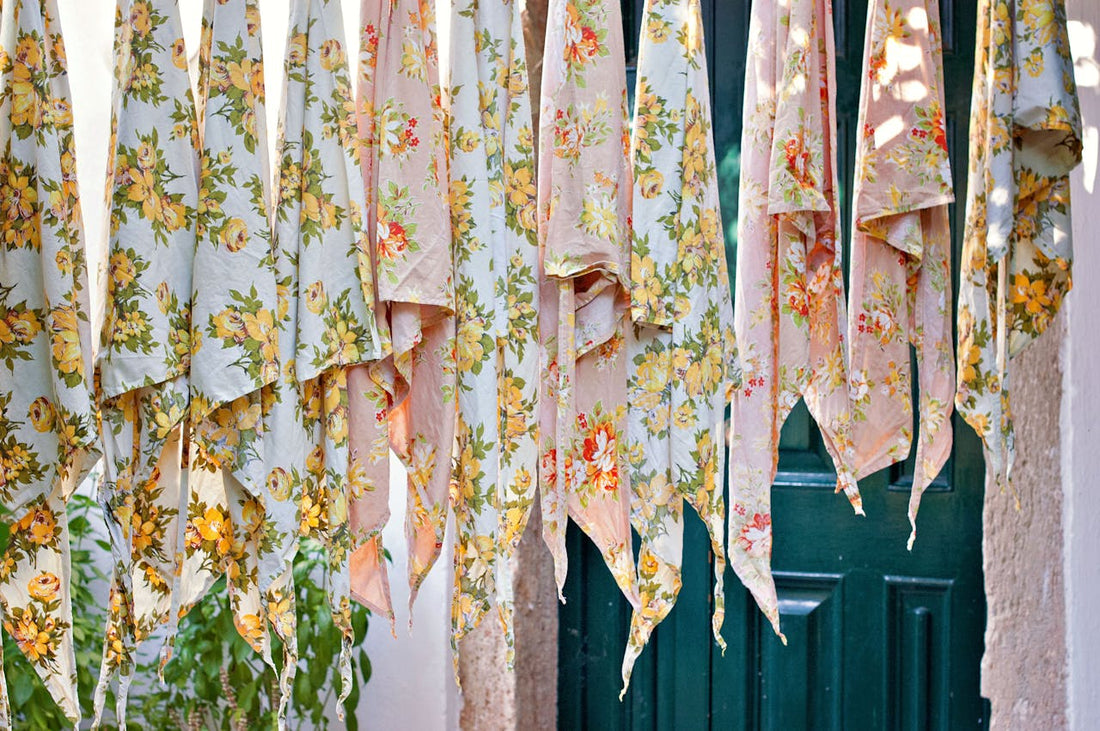
Fabric printing is a process of applying color, patterns, or designs to textiles using various methods. Below are common fabric printing techniques explained in English:
1. Direct Printing
Process: The most common method where dyes or pigments are directly applied to the fabric using screens, rollers, or digital printers.
Advantages: Versatile, cost-effective, and suitable for simple to complex designs.
Disadvantages: Limited color vibrancy on dark fabrics.
Applications: Cotton, polyester, and blended fabrics for apparel and home textiles.
2. Discharge Printing
Process: A bleaching agent is used to remove color from dyed fabric, creating a design by "discharging" the original dye. New colors can be added to the bleached areas.
Advantages: Soft finish with vibrant contrasts on dark backgrounds.
Disadvantages: Requires pre-dyed fabric; not eco-friendly due to chemicals.
Applications: T-shirts, sweatshirts, and heavy fabrics.
3. Resist Printing
Process: A resist agent (e.g., wax, paste) is applied to prevent dye penetration in specific areas. Common subtypes include **Batik** (wax resist) and **Tie-Dye**.
Advantages: Unique, artistic effects with organic patterns.
Disadvantages: Labor-intensive and time-consuming.
Applications: Artisanal textiles, bohemian fashion.
4. Digital Printing
Process: Uses inkjet technology to print designs directly onto fabric from digital files.
Advantages: High detail, unlimited colors, and quick prototyping; ideal for small batches.
Disadvantages: Higher cost for large-scale production.
Applications: Custom fashion, upholstery, and photo-realistic designs.
5. Heat Transfer Printing
Process: Designs are printed on transfer paper and then heat-pressed onto fabric.
Advantages: Sharp details and vibrant colors; works well on synthetic fabrics.
Disadvantages: Less durable on natural fibers like cotton.
Applications: Sportswear, promotional items, and polyester-based textiles.
6. Screen Printing
Process: A mesh screen is used to transfer ink onto fabric. Each color requires a separate screen.
Advantages: Durable, vibrant results; cost-effective for bulk orders.
Disadvantages: Setup costs and time increase with color complexity.
Applications: T-shirts, posters, and industrial textiles.
7. Roller Printing
Process: Engraved metal rollers apply dye to fabric in a continuous process.
Advantages: High-speed production for large quantities.
Disadvantages: Limited design flexibility and high setup costs.
Applications: Mass-produced patterned fabrics like floral bedsheets.
8. Block Printing
Process: Hand-carved wooden or metal blocks are dipped in dye and stamped onto fabric.
Advantages: Traditional, handmade aesthetic.
Disadvantages: Slow and inconsistent for large-scale use.
Applications: Ethnic textiles, artisan crafts.
9. Sublimation Printing
Process: Dye is converted into gas under heat, bonding with synthetic fibers (e.g., polyester).
Advantages: Fade-resistant, seamless designs.
Disadvantages: Only works on synthetic fabrics.
Applications: Activewear, flags, and sublimation-friendly textiles.
10. Flock Printing
Process: Adhesive is applied to fabric, and tiny fibers (flock) are electrostatically attached to create a velvet-like texture.
Advantages: Tactile, 3D effects.
Disadvantages: Limited wash durability.
Applications: Decorative fabrics, logos, and apparel accents.
Conclusion
The choice of printing method depends on fabric type, design complexity, durability requirements, and production scale. Innovations like digital printing are revolutionizing customization, while traditional methods like block printing preserve cultural craftsmanship.