How Cotton Becomes Cloth
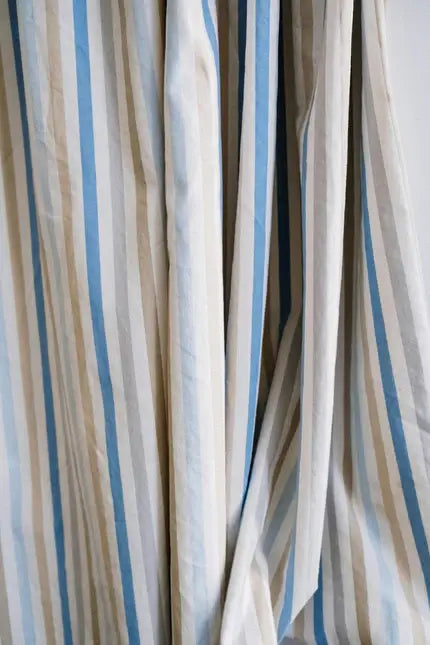
Cotton, one of the world’s most versatile and widely used natural fibers, undergoes a fascinating transformation before becoming the soft, durable fabric we know. This journey from fluffy plant bolls to finished cloth involves several carefully orchestrated steps. Let’s explore how cotton is turned into cloth.
1. Harvesting the Cotton
The process begins in the fields. Cotton plants produce bolls, which burst open when ripe, revealing the fluffy white fibers inside. Modern harvesting is typically done using mechanical pickers or strippers, which efficiently collect the cotton bolls. In some regions, hand-picking is still practiced to preserve fiber quality.
2. Ginning: Separating Fiber from Seed
After harvesting, raw cotton (called *seed cotton*) contains seeds, stems, and debris. It’s sent to a **cotton gin**, where machines separate the fibers from the seeds—a process known as *ginning*. Modern gins use saws or rollers to cleanly extract the seeds (which are later used for oil or livestock feed). The result is *lint*—pure cotton fibers pressed into large bales for transport.
3. Cleaning and Carding
At the textile mill, cotton bales are opened and fluffed. The fibers pass through cleaning machines to remove residual impurities. Next, they undergo **carding**: a mechanical process where fibers are aligned into a thin, continuous web. This web is condensed into a loose rope-like strand called a *sliver*. Carding ensures uniformity and removes shorter fibers, creating smoother yarn.
4. Spinning: Creating Yarn
The sliver is drawn out and twisted during **spinning** to add strength. Traditional *ring spinning* uses rotating spindles to produce fine, sturdy yarn, while newer methods like *open-end spinning* create bulkier threads faster. The spun yarn is wound onto bobbins or cones, ready for weaving or knitting.
5. **Weaving or Knitting
Weaving: Yarn is interlaced on looms to create woven fabric. Horizontal (weft) and vertical (warp) threads cross each other, forming textiles like denim, canvas, or satin. Modern automated looms can produce intricate patterns efficiently.
Knitting: For stretchier fabrics (e.g., t-shirts), yarn is looped together using knitting machines. This method allows for flexibility and speed.
6. Finishing: Perfecting the Fabric
The newly made cloth undergoes treatments to enhance its properties:
Bleaching: Removes natural tints for a clean base.
Dyeing/Printing: Color is added either by immersing yarn/fabric in dye or printing patterns directly.
Mercerization: Treating cotton with alkali to increase luster and strength.
Softening or Sanforizing: Processes to prevent shrinkage and improve texture.
Finally, the fabric is inspected for quality, graded, and rolled for distribution to manufacturers.
Conclusion
Transforming cotton into cloth is a blend of age-old techniques and modern innovation. Each step—from harvesting to finishing—ensures the final product meets demands for comfort, durability, and style. Next time you slip on a cotton shirt or snuggle into cotton sheets, remember the remarkable journey that brought this humble plant to your home.
*Cotton’s legacy as the “fabric of our lives” is woven into every thread.* 🌾🧵